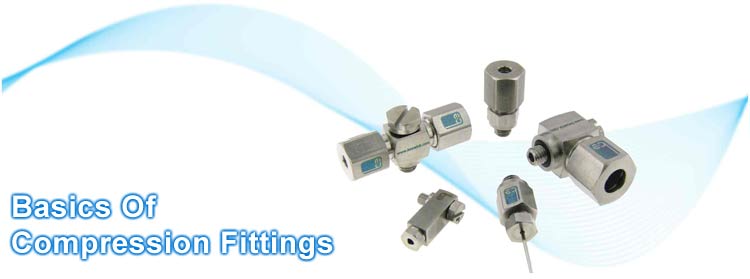
Introduction to Compression Fittings
Compression fittings are one of the most common and versatile methods of connecting metal or hard plastic tubing. Particularly useful for their extreme temperature and pressure capabilities, and their compatibility with aggressive fluids, compression fittings can be seen in systems varying from gas lines in refineries, to the plumbing under your sink.
Miniature compression fittings are found in applications ranging from chromatography and bomb detection instruments, to medical devices and inkjet printing. Whether it’s the water heater in your home or a pipe transporting hazardous chemicals, all compression fitting applications have several traits in common: they require easy assembly, long life, and absolutely no leaks.
Compression fitting assemblies vary in design from manufacturer to manufacturer, but are all made up of the same three basic elements: a compression nut or screw, one or more ferrules, and a compression fitting body. The functioning principle of each component also remains more or less the same between designs: tubing is inserted into the end of the fitting, and the nut/screw is tightened, forcing the ferrule(s) into the fitting body. As the ferrule(s) moves axially into the fitting body, the body’s angled shape radially compresses the end of the ferrule onto the outer diameter of the tubing. It is this radial compression that creates the leak tight seal between the fitting, ferrule, and tubing, and gives the compression fitting its name.
The success of compression fittings in a given application can depend on a number of factors. Chief among these are fitting and ferrule design, tubing selection, and installation procedure.
Ferrules
The ferrule is the primary sealing component of a compression fitting assembly, and they can be found in a wide variety of materials ranging from stainless steel to graphite. The majority of ferrules in the marketplace however, are manufactured from metals. Metal ferrules are attractive because they are stable over a wide temperature range, and they can bear compressive loads without relaxing. Typically, metal-to-metal seals are considered leak-prone (for example, metal pipe threads are often reinforced with pipe tape). Ferrules however, are specifically engineered to create an optimal seal against both the tubing and the fitting body. Some of the key factors of the ferrule design include:
Ferrule Shape
The shape of both the ferrule and the mating angle of the fitting body are critical factors in the reliability of a compression seal. Both components must be tapered in a manner that allows the ferrule to compress properly as the nut is tightened, while maintaining axial alignment with the tubing. Additionally, the relative angles of the ferrule and the fitting body will determine how much linear motion is converted into radial compression, and what level of contact (“line contact” or “surface contact”) is made with the tubing. A uniform, “line contact” compression around the entire circumference of the ferrule will create the most reliable seal. To this end, it is also important that the ferrule have a sharp forward edge.
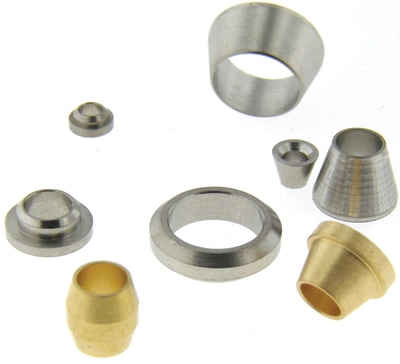
One Piece vs. Two Piece Ferrules
Most basic compression fittings contain a single ferrule. Single ferrule designs minimize the total number of components, and work reliably when fabricated from softer materials (plastic or brass for example). With harder materials like steel however, torque is often transferred from the compression nut to the ferrule as the nut is tightened. The resulting rotation can cause the ferrule to compress asymmetrically, or to shift over time due to residual torque. In stainless steels, rotation of the ferrule can also produce galling and cause permanent leaks. Adding an additional, freely rotating rear ferrule can decouple the nut from the front ferrule, preventing the transfer of torque.
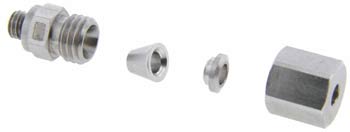
Asymmetrical vs. Symmetrical Ferrules
One piece ferrules are often available as asymmetrical or symmetrical. Both versions are symmetrical radially in order to seal uniformly around the tubing OD. Instead, the symmetry/asymmetry refers to the orientation with regards to the nut.
An asymmetrical ferrule is cone shaped, and can only be placed into the fitting body in one direction (usually with the tip of the cone facing into the fitting body). Symmetrical ferrules look like two cones back-to-back, and can be placed into the fitting body in either direction. This increases the ease of assembly in applications where many fittings are used, and assembly time is critical.
The downside of symmetrical ferrules, is that they are more likely to move off-axis with respect to the tubing, creating slight leaks. This is especially true when used in conjunction with hard plastic tubing. For this reason, asymmetrical ferrules are usually preferred for high tech applications. Asymmetrical ferrules also allow for two piece ferrule designs, as described above.
Tubing
Compression fittings are most commonly used with hard tubing because the tubing wall must be rigid enough to resist the compression forces applied by the ferrule. Common choices include metallic tubing (such as stainless steel or copper) and stiff plastic tubing (such as PEEK, nylon, Teflon®, Kynar®, or polyethylene).
The use of softer tubing (such as polyurethane or vinyl) is not normally recommended with compression style fittings because the tubing wall is likely to collapse, or move away from the ferrule. This negates the holding power of the ferrule, and can also prevent the ferrule from making a leak-tight seal around the full diameter of the tubing. If there is a particular design issue (for example, a tight bend radius) that necessitates softer tubing, it is important to reinforce the tubing wall. Some manufacturers offer tubing inserts for this purpose. The tubing insert, usually made of metal, is pressed into the soft tubing, and supports the tubing wall so that it will not collapse as the ferrule is compressed.
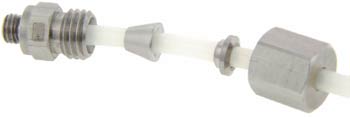
The physical and chemical characteristics of various tubing materials must be taken into consideration when choosing the best tubing for a given application. It is good practice to seek technical support from a tubing supplier when working on a new design. Key factors include: pressure and temperature extremes, environmental conditions, vibration conditions, fluid compatibility, and minimum bend radius. In addition to these general considerations, there are several more specific factors to consider regarding compression fitting assemblies, such as:
Teflon (PTFE) Tubing
PTFE tubing is a popular material choice for tubing because it is resistant to most chemicals, handles relatively high pressure, is low out-gassing, and is more flexible than metallic tubing. One key design factor when using this kind of tubing is its tendency to “cold flow”, or deform away from a compressive load. This can cause leaks to develop over time, as the tubing wall begins to creep (cold flow) away from the ferrule. The cold flow issue is exacerbated when the tubing is exposed to high temperatures, and can occur even when fittings are properly installed and initially leak free.
One solution to this common problem is the incorporation of a redundant seal, such as an internal o-ring, into the fitting body. This secondary sealing element makes a radial seal against the outside diameter of the tubing, independent of the seal created by the ferrule. This is a “belt and suspenders” design approach, but has proven highly effective in solving the cold flow leakage issue.
Metal Tubing
The way in which metal tubing is produced can have a significant effect on its performance with compression fittings. Tubing should be smooth and free of roughness or extrusion lines that can create a leak path past the ferrule. Furthermore, tubing that has been stored in coils can often have an asymetrical diameter, preventing even compression. While an elastomeric seal can deform to match these slight variations, the metal-to-metal seal of a compression fitting is less forgiving. It is also important that the end of each section be squarely cut, to allow the tubing to sit symmetrically in the fitting body.
Installation
Installation instructions for compression fittings vary depending on the manufacturer and the specific fitting design. Care should be taken to follow the assembly procedures recommended by the manufacturer. There are however, several common elements to the installation procedure for nearly all compression fittings:
Distance vs. Torque
Typically the procedure for tightening a compression fitting is specified using the rotation of the nut as the key metric, rather than torque. Compression nuts are threaded, meaning that the number of rotations of the nut is directly correlated to the linear compression of the ferrule, based on the thread’s pitch. Torque, on the other hand, can vary greatly, depending on fitting and ferrule material, lubrication, degree of galling (for stainless fittings), and other factors.
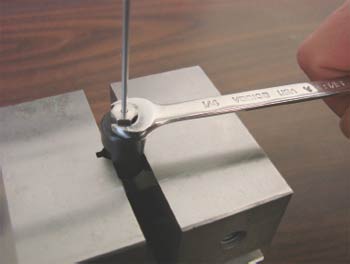
Tighter is Not “Better”
Often when assembling fittings, assemblers and engineers assume that “tighter is better”. This does not hold true for compression fittings. As described in the “Ferrules” section above, the optimal seal is created by a line contact between the ferrule and the tubing. Insufficient tightening of the compression nut will not deform the ferrule enough to create this contact, but over-tightening will deform the ferrule too much, creating a surface contact. A surface contact weakens the seal and often results in leaks
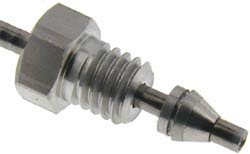
Disassembly and Re-Assembly
The ease of assembly and disassembly is one of the reasons why compression fittings are so widely used. Disassembly involves simply loosening the compression nut or screw. Re-assembly can be accomplished in a similar manner to the initial assembly, although typically fewer turns of the nut are required, since the ferrule is already swaged to the tubing. It is important to note however, that compression fittings can only be disassembled and reassembled a few times before either the ferrules and/or the fitting body should be replaced, to ensure a leak-tight seal.
Mixing and Matching Components
Even if components from two different manufacturers look similar externally, they will often differ in key internal dimensions, such as ferrule/body taper, ferrule length, and thread size and pitch. Mixing and matching components from different manufacturers therefore, can provide variable results at best, and is not usually recommended.
Application Considerations
Compression fittings are often selected for reasons beyond just leak-free sealing and ease of use. In many applications, high pressures and temperatures necessitate the use of hard tubing, which is incompatible with many other types of fittings. In other applications, such as laboratory instruments, concerns over contamination make the sterility and low out-gassing properties of stainless steel tubing and compression fittings attractive. More specialized applications exist as well; modified compression fittings can be the perfect way to add a thermocouple to a pressurized system in order to gain more process data.
Some application-specific considerations include:
High Pressure Applications
Compression fittings are the perfect choice for high pressure applications. In combination with a high pressure tubing material like steel, large compression fittings can often be used at pressures in excess of 10,000 psig. Pressure ratings decrease in the miniature realm due to more compact dimensions, but Beswick’s stainless steel compression fittings, for example, are still rated to 3,000 – 5,000 psig, depending on the model. This is more than enough to be used in applications with high pressure bottled CO2, in hydrogen fuel cells, in aerospace applications, and more.
The key to using compression fittings at high pressure, especially with gases, is the integrity of the ferrule seal. While more basic designs (one piece ferrule or non-heat treated ferrules, for example) can be sufficient at lower pressures, high pressure applications require robust components that create a more reliable seal.
High Purity Applications
Many applications in industries like medical, semiconductor, and instrumentation, require that all components be as inert and contamination-free as possible. Compression fittings facilitate these applications greatly. Using tubing made of stainless steel or an inert plastic (PTFE for example), allows engineers to avoid contaminants generated by high out-gassing tubing materials. Furthermore, compression nuts and ferrules are often all metal, and can be autoclaved, cleaned, or sterilized more easily than fittings containing plastics or internal elastomers.
One factor to plan for in these high purity applications is galling. Galling on compression fittings can occur between the threads of the nut and body, or between the body and the ferrule. Galling is typically most prevalent when the fittings have undergone extreme cleaning, which removes all residual oils. Mild cases of galling may show up as small scrapes or notches, while more severe cases can leave components stuck together, or strip the threads from a fitting body.
It is crucial in these applications that ferrules designed to resist galling are used. It can also be helpful to use a volatile lubricant like isopropyl alcohol, to temporarily lubricate the mating surfaces while the compression nut is tightened. The alcohol will lubricate the stainless steel surfaces during assembly, and then evaporate completely, leaving no residue or contaminants behind.
Conclusion
Compression fittings are widely used across a number of industries, and can be an asset in almost any fluid power design. Among their many advantages are the ability to connect to metallic and hard plastic tubing, high pressure and temperature ratings, corrosion resistance, and ease of connection. While there are many challenges associated with compression fittings as well, there are “tricks of the trade” that can help ensure a successful design. No two applications are exactly the same! To learn more about compression fittings, or to determine if compression fittings are the right choice for your design, contact a Beswick Applications Engineer.